
News Coverage
• Surgical cotton made in nagpur,Times of India
NAGPUR: Not every one dreams big. But Prakash Rathi, a small scale industrialist from the city, always raised the bar and worked hard to realize it too.With just a diploma in pharmacy to his credit in the name of professional education, Rathi once went from shop to shop on his cycle selling surgical cotton to medical stores all over the city. Now he owns one of the largest manufacturing units of surgical cotton in the country. He continues to harbour bigger dreams and is working hard to reach the top by setting up the biggest dedicated unit at the cost of Rs 2 crore with modern technology in Ambadi village in Badoda industrial area in Kamptee tehsil on Bhandara Road.Starting his career with repacking basic chemicals like glycerine and boric acid, Rathi entered into the business of selling surgical cotton after with a loan of Rs 5000 from a friend visiting a small cotton unit of his cousin in Gwalior. As his sales increased, he set up a small industry using the available technology in 2004 with financial support worth Rs 25 lakh from the Khadi Village Industries Corporation.But there were technical hitches which affected production every now and then. A motivated Rathi did not give up. He researched on the latest technology in India and abroad in countries like China.
To his surprise, he found that even China lagged behind in this field."I was amazed to see that the local manufacturers in China did not produce quality surgical cotton. Back home the bigger manufacturers who didn't want any competitors did not share information on their technology. I managed to gather some information from CIRCOT in Mumbai and Coimbatore. But that was not enough. So I modified my machinery myself and got it fabricated. My new unit can now manufacture and sell 5 tons of surgical cotton daily," said Rathi's father, a small trader of gunny bags in Itwari, never believed that his son could do big business. But his mother always motivated him. It is her trust that Rathi says has brought him to this level where he has a turnover of over of Rs 1.5-2 crore. He also has support and guidance from his friend, philosopher and guide Ashok Thakre, and Keshav Kranthi, the director of the Nagpur-based Central Institute for Cotton Research.The modified process developed by Rathi will reduce the labour need from about 40-50 men to just 4-5 persons. In fact, his unit will be able to produce cotton beginning from just 2 inches to 40 inches which can be used for making quality mattresses too. "All plants including leading manufacturers like the Ramaraju Surgical Cotton Mills Ltd in Tamil Nadu and Jaycot Industries in Hyderabad use the old technology. My industry will use latest technology like vacuum for removing water," claimed Rathi.Very few know that surgical cotton is made from a special cotton variety called as Bengal Desi Cotton grown extensively only in India (18 districts near Ganganagar in Rajasthan) and adjoining areas in Pakistan. Rathi tells that almost all major surgical cotton manufacturers in world look forward to procuring this cotton as it has almost all the characteristics required for good quality surgical cotton like liquid absorbency, fibre quality (strictly 18 inches), minimum wax and micronaire value of 5.The manufacturing process basically involves opening and cleaning of pressed cotton bales, boiling it at 90 degrees Celsius with water and chemicals to give it white colour (raw Bengal desi cotton is almost brownish), removing water completely, drying it, lapping, carding, rolling, cutting and packaging. Rathi has also improvised the cleaning process to remove sulphated ash, biggest contaminant in cotton and the vacuum process for draining water before drying the cotton."At present I am one of four biggest suppliers to all medical colleges and government hospitals in the state.
• Surgical cotton gets the boost,Indian Express
Surgical cotton or absorbent cotton is in great demand all over the world, but with desi cotton — considered ideal raw material for it — being edged out, manufacturers have been banking heavily on regular American cotton.
The Central Institute for Cotton Research (CICR) here is now working towards partnering with farmers and absorbent cotton manufacturers for promoting organic desi cotton as raw material.
The CICR has already started producing desi cotton seeds to be distributed to a select group of farmers — who are going to have assured buyers offering good price.
"We have discussed it with many manufacturers. They are ready to pay up to Rs 4,000 per quintal. For now, we will emphasise on the idea in Vidarbha and parts of Madhya Pradesh where farmers around villages near surgical cotton units will be encouraged to produce organic desi varieties with an assured high price," said CICR director Keshav Kranthi.
One such unit has come up recently near Nagpur.
Prakash Rathi, owner of Rathi Chemicals, is partnering in the venture with CICR. The Central Institute for Research in Cotton Technology (CIRCOT), Mumbai, will be another stakeholder in the process of converting raw cotton into finished product.
"As of now, the companies in India are using Bengal Cotton, a desi variety being produced mainly in north-east and Rajasthan, to manufacture surgical cotton. But it requires chemical treatment. What we are looking at is having organic desi varieties that will eliminate the need for chemical treatment. We have certain microbes that can be used," Kranthi said.
Another advantage with desi cotton is its low input cost. "It requires less inputs since it has traditionally come to withstand hard Indian conditions," Kranthi said.
He says because organic cotton is devoid of chemicals, it is ideally the most-suited cotton for manufacturing absorbent cotton. "And anything organic has a great demand in Europe, so the produce will also have a great export potential," he adds.
During the next planting season, CICR is planning to have 500 hectares of dedicated desi organic area in Vidarbha.
In India itself, the demand for surgical cotton is up to 20 lakh bales per year, Kranthi adds.
"Till about 7-8 years ago, India had about 20 lakh hectares of desi cotton area. Now, it has been reduced to just about 1 lakh hectare," Kranthi said.
Desi varieties have been grown in India for centuries and had come to stay as most sturdy varieties till they were slowly replaced by American cotton and now by Bt cotton. Desi varieties, with short-staple fibre, which can be grown with organic inputs, are considered ideal for manufacturing absorbent cotton.
Ideally, surgical cotton requires coarse textured lint with a fibre length of approximately 18 mm so that these can easily be arranged into layers for surgical use. Micronaire is an index of fineness or coarseness of the fibre and the preferred micronaire value for surgical use is 6.5 to 8.0.
"CICR has a rich repository of desi cotton that will be utilised for popularising this type of cotton. Several varieties like Lohit, LD-133, RG-8, LD-327, DS-21, LD-491, HD-11 have been released by the public sector in the past with fibre quality parameters suitable for surgical cotton," Kranthi said.
QUALITY

Quality is our forte and we take several initiatives to maintain the standard of our products throughout production and post production stages. Our Absorbent Cotton, Absorbent Gauze and Roller Bandages are checked on the basis of well-defined parameters before offering to the clients.

NEWS COVERAGE

Surgical cotton made in nagpur, Times of India
NAGPUR: Not every one dreams big. But Prakash Rathi, a small scale industrialist from the city, always raised the bar and worked hard to realize it too

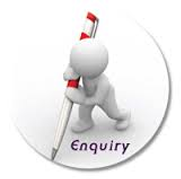